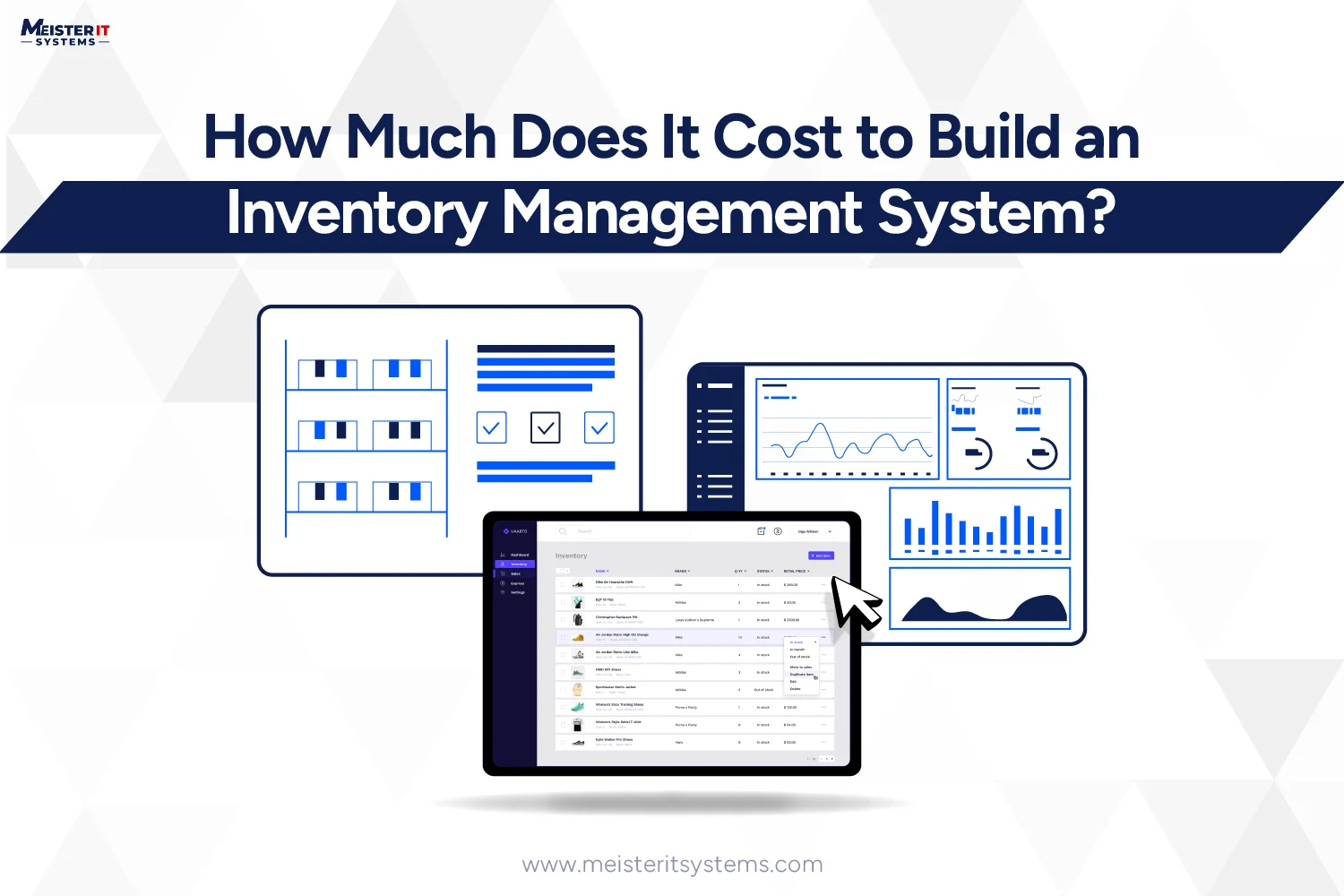
Introduction
Building an inventory management system is a significant investment that can transform how you handle your stock to streamline operations. However, one of the most common questions businesses ask is, “How much does building an inventory management system cost?” The answer depends on several factors, from the complexity of features to the technology stack and development approach.
In this article, we will break down the key cost factors and provide insights to help you estimate the budget for building an inventory management system tailored to your business needs. Whether you are a small business or a large enterprise, understanding these factors will help you make an informed decision.
But wait, before jumping into the cost of building an inventory management system, it would be helpful first to understand what exactly it is.
So, let us get started!
What Is an Inventory Management System?
Almost 43% of small businesses either do not track their inventory or rely on outdated methods like spreadsheets.
This often results in issues like overstocking or understocking, leading to inefficiencies, lost revenue, and customer dissatisfaction. Effective inventory management is crucial for avoiding these problems, and that is where an Inventory Management System comes into play. It is a software solution designed to help businesses efficiently track, manage, and control their inventory across multiple locations.
Features of Inventory Management System
Your business’s efficiency depends on the inventory management system you choose for your operations and the features that are integrated into the system.
So, let’s talk about the features that make IMS productive for all businesses.
- Real-time Tracking: This helps businesses see stock availability in multiple locations, allowing them to restock items before running out. Real-time tracking helps businesses improve their supply chain by spotting trends in inventory movement.
- Order Management: By automating the process of creating, tracking, and managing purchase orders and reorders, inventory management systems ensure quick restocking and reduce manual errors. This ensures timely restocking, reduces dependency on manual entries, and minimises human errors. Additionally, the system’s intelligence order handling allows for smoother operations by setting reorder thresholds and managing supplier relationships efficiently.
- Barcode/RFID Integration: The use of barcodes can reduce human error by 43.5%. Barcodes help track inventory more quickly and accurately, improving inventory precision and decreasing errors. Integrating barcodes or RFID technology also allows for real-time visibility of inventory levels, helping businesses make faster, more informed decisions.
- Demand Forecasting: The system uses past sales data and analysis to predict future inventory needs. It maintains optimal stock levels, reducing the risk of both stockouts and overstocking. Effective demand forecasting not only improves customer satisfaction but can also lower inventory holding costs by up to 10%, ensuring efficient capital allocation.
- Stock Alerts: Receive notifications when stock levels are low or excess stock is present. By getting stock alerts, businesses can quickly reorder products to meet customer demand and avoid lost sales. Conversely, alerts for excess stocks help businesses implement strategies to reduce holding costs and prevent overstock.
- Inventory Valuation: It is important to calculate the total value of your inventory based on current stock levels and product costs to assist with financial management. It is crucial to accurately assess the financial health of your business and make informed decisions. By regularly updating inventory valuations, businesses can ensure that their balance sheets reflect the real-time values of their assets and liabilities.
- Reporting & Analytics: The system generates real-time, data-driven reporting on inventory levels and sales performance, such as stock turnover and shrinkage rates. Advanced analytics provide actionable data that enable strategic purchases, inventory restocking, and stock management. This helps to discover trends and optimise inventory for long-term growth.
If you are unsure how to build an effective inventory management system and want to benefit from it, check out our comprehensive guide on building an inventory management system.
Factors Influencing the Cost of Inventory Management System
Implementing an inventory management system can streamline your operations and help you better manage your inventory. However, building your own inventory management system can be expensive as the cost depends on several factors. So, let us discuss them below in detail.
Features and Functionality
The desired features and functionality are the primary factors influencing the cost of developing a custom inventory management system. More complex systems with advanced features like multi-location support, AI-powered forecasting, and integrations with other software will naturally require a higher investment.
Here is a breakdown of estimated costs based on feature complexity:
- Simple Systems: For small businesses needing basic features like real-time tracking, simple reporting, and single-location support, the cost typically ranges from £10,000 to £50,000.
- Advanced Systems: Businesses requiring more sophisticated capabilities, such as multi-location tracking, advanced analytics, AI-driven forecasting, and integrations with other systems, can expect costs to range from £50,000 to £200,000 or more.
To effectively balance cost and functionality, carefully consider your specific business needs and prioritise features that will provide the most value.
Development Approach: Custom vs. Off-the-Shelf Solutions
Choosing between a custom-built and off-the-shelf inventory management system is a critical decision. Each approach offers distinct advantages and costs.
Off-the-Shelf Software:
- Pros: Ready-to-use, often cheaper (typically £5,000 to £30,000 annually), and quicker to implement.
- Cons: Limited customisation options, may not perfectly align with specific business needs.
Custom-Built Solutions:
- Pros: Tailored to exact requirements, offers greater flexibility.
- Cons: Higher initial investment (starting at £50,000, often exceeding £200,000), longer development time.
The best choice depends on your business’s unique needs, budget, and timeline. Consider factors such as the complexity of your operations, scalability requirements, and the importance of customisation.
Technology Stack
Did you know? AI-enabled supply chain management improves logistics costs by 15%, inventory levels by 35%, and service levels by 65%.
This integration of a modern technology stack behind the inventory management system (IMS) can significantly impact the development cost. However, it can significantly increase the cost of developing inventory management systems. Here is the breakdown of the technology stack influencing the development cost.
- Server-side tools: Programming languages like Node.js, Python, or Java can be used for the backend, or server-side, of the system. Each language has its strengths and weaknesses, which can affect how fast and expensive it is to develop the system.
- User interface tools: Frameworks like React or Angular can be used to create the user interface, or what you see when you use the system. The more complex the interface, the more time it will take to build, which will increase the cost.
- Data storage: SQL databases are often used, while some systems may prefer NoSQL options like MongoDB. The choice depends on how you want to store and access your data.
- Hosting and server costs: Whether you choose to host your system in the cloud or on your own servers will affect how much it costs to maintain. Cloud hosting can be cheaper upfront but may have ongoing costs, while on-premise hosting requires a larger initial investment but can give you more control.
Development Team Size and Location
The size and location of your development team are crucial factors in determining the cost of building an inventory management system. Opting for an in-house team offers greater control and collaboration but comes with higher costs, typically ranging from £100 to £200 per hour. On the other hand, outsourcing to more cost-effective locations can lead to reduced expenses, with rates between £39 and £106 per hour while maintaining quality standards. The team’s size also plays a significant role—larger teams can expedite the project timeline but will increase overall costs. Striking the right balance between team size and outsourcing options can help manage costs without compromising quality.
Third-Party Integrations
Integrating your Inventory Management system with other systems such as ERP, CRM, or e-commerce platforms (e.g., Shopify, Magento) can significantly impact costs. Each integration may cost between £5,000 and £30,000, depending on its complexity.
Maintenance and Support Costs
Regular upgradation and maintenance are crucial to keep the system effectively running. Which increases the development cost of your inventory management system. Here are estimates of maintenance and support costs:
- Maintenance Fees: Typically, 15% to 20% of the total development cost is set aside annually for maintenance.
- Support Services: Depending on whether you opt for 24/7 or limited support, prices can vary. Expect to pay around £1,000 to £10,000 annually for support services
Apart from these costs, it is crucial to consider the long-term value of regular maintenance and support. Proper maintenance ensures that your inventory management system remains secure, functional, and up-to-date with the latest technological advancements. Neglecting maintenance can lead to system downtimes, vulnerabilities, and higher costs in the future. By budgeting appropriately for these services, you can avoid unexpected expenses and ensure smooth operations over time.
Estimated Cost Breakdown To Build Inventory Management System
Real-time visibility is a game-changer for your business. 72% of retailers plan to implement it using automation, sensors, and analytics. However, the cost of adding this feature to your inventory management system varies depending on your business size and specific needs.
Below is the breakdown of the estimated costs of building different aspects of an inventory management system:
Features | Estimated Cost |
---|---|
Basic Features (inventory tracking, user roles, reporting) | £20,000 – £50,000 |
Advanced Features (multi-location support, analytics, integrations) | £50,000 – £200,000 |
Real-time Visibility (automation, sensors, analytics) | £30,000 – £100,000 |
Customisation for Large Enterprises (AI, scalability, extensive integrations) | £200,000+ |
Employee Training (varies by team size) | £500 – £5,000 |
Data Migration (depends on data volume/complexity) | £1,000 – £10,000 |
Hardware Upgrades (barcode scanners, RFID tech) | £5,000 – £50,000 |
Ongoing Maintenance & Support (annual, post-launch) | 15% – 20% of total development |
Before proceeding, carefully evaluate your business needs and budget to ensure successful implementation, especially if considering features like real-time visibility and advanced analytics, which can significantly affect costs.
How to Reduce the Cost of Building an Inventory Management System?
Real-time visibility is a game-changer for your business. 72% of retailers plan to implement it using automation, sensors, and analytics. However, the cost of adding this feature to your inventory management system varies depending on your business size and specific needs.
Building your inventory management system is an expensive deal because it depends on several factors discussed earlier in the article. However, there are some strategies to reduce the development cost of the Inventory Management System.
Here are some:
- Focus on the Basics: Start with core features that align with your business needs, rather than developing a complex system with unnecessary functions that can drive up costs.
- Outsourcing to Experts: Rather than building an internal team, outsourcing to a reliable Inventory Management System development partner results in cost savings on salaries, recruitment, and overhead.
- Leverage Open-Source Solutions: Development teams can customise open-source inventory management software to meet specific requirements, providing a cost-effective alternative to building from scratch.
- Phased Development: Implement the system in phases, prioritising essential features initially. This approach allows for spreading out costs and investing in additional capabilities only when needed.
- Cloud-Based Solutions: A cloud-based system can reduce hardware expenses, eliminating the need for costly on-premise infrastructure and ongoing maintenance.
By outsourcing the development of your inventory management system, you can minimise upfront costs while ensuring a high-quality, tailored solution.
Conclusion
Building an inventory management system is a significant but worthwhile investment for businesses looking to optimise their operations. The total cost depends on factors such as the features you need, the development approach you choose, and ongoing maintenance. By understanding these cost drivers, you can make an informed decision and develop a solution that fits your business goals and budget.
Ready to take the next step but worried about the cost? Then hiring a partner like MeisterIT Systems will be cost-friendly, instead of hiring your own team.
Contact us today to get tailored advice for your business needs!